Lubricant efficiency on a new level.
Lubricant efficiency on a new level.
The OMC₂ additive technology
Market requirements are changing due to rapid economic developments, global competition and technological progress. This challenges tribology and lubrication technology to develop ever more efficient and comprehensive lubricant solutions. A typical requirement is the further reduction of surface friction to increase energy efficiency and optimise the smooth running of motion sequences - even at extreme temperatures and under enormous loads. A further increase in power density is also required. Finally, technical designs should be as small and light as possible and extremely efficient. TUNAP offers a comprehensive solution for these different requirements: OMC₂ additive technology (OMC: Organic Molybdenum Compound).
OMC2 technology in film
When you view and play embedded videos on www.tunap.com, the provider (YouTube) may be able to store your access and analyze your behavior. If you activate the content, i.e. agree to view and play it, a cookie is placed on your computer to record that you have agreed to this in your browser. This cookie does not store any personal data.
For more information, please see our privacy policy and cookie page.
You can also use this link to access the video directly on the plattform of the provider: https://youtu.be/5oB31qIqikw
Application advantages of the OMC₂ technology
Our OMC₂ additive technology offers various advantages compared to conventional lubricants:
It enables a longer service life with lower lubricant consumption. Lower frictional heat ensures reduced energy consumption and helps to reduce the environmental impact and make a sustainable contribution to CO₂ reduction.
The lower maintenance and repair costs also increase machine availability. This in turn results in cost savings for disposal. All in all, this means significant cost and resource savings for users.
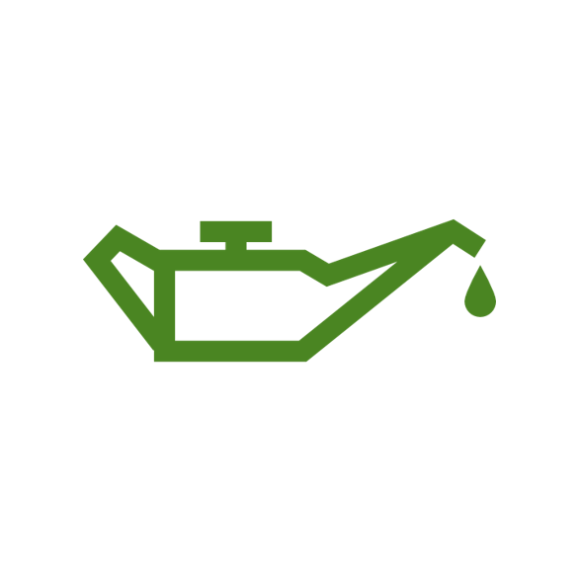
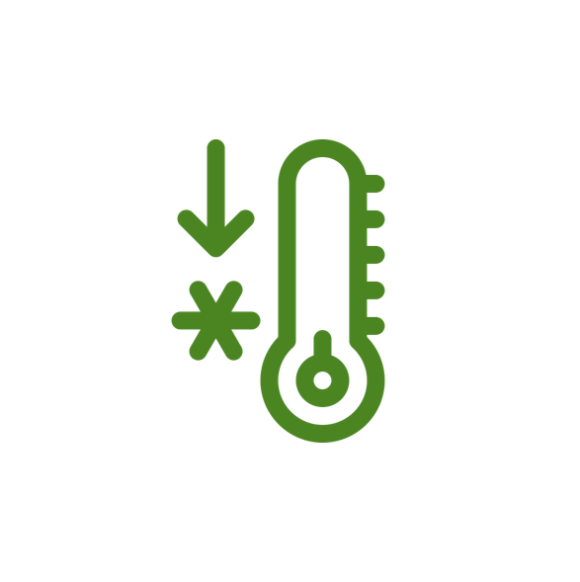
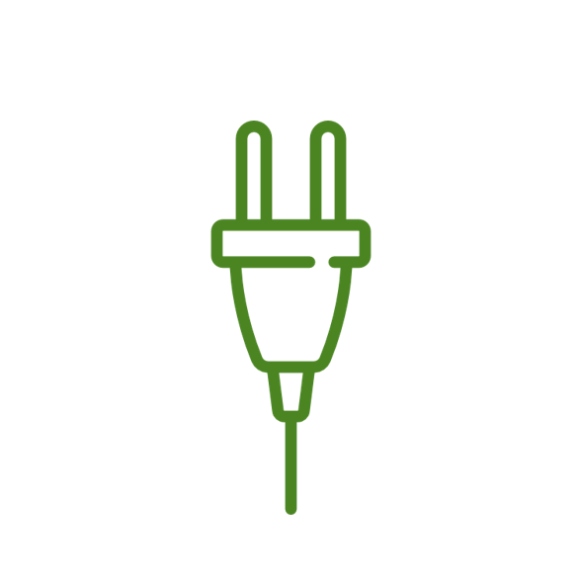
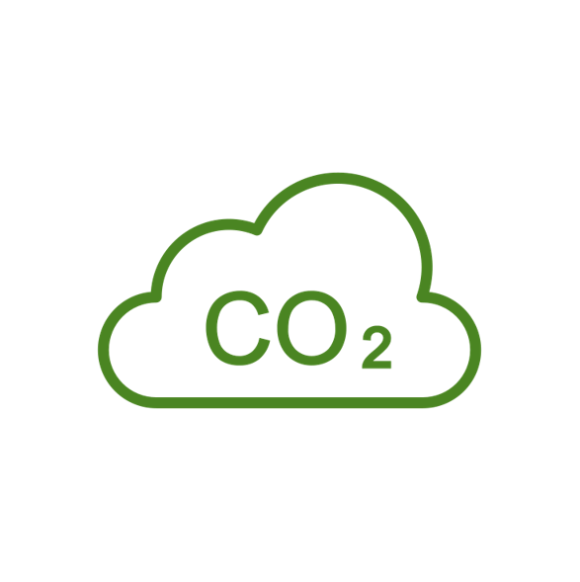
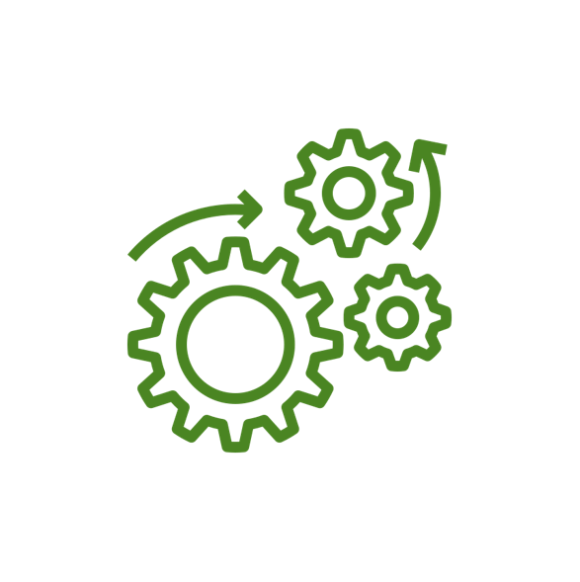
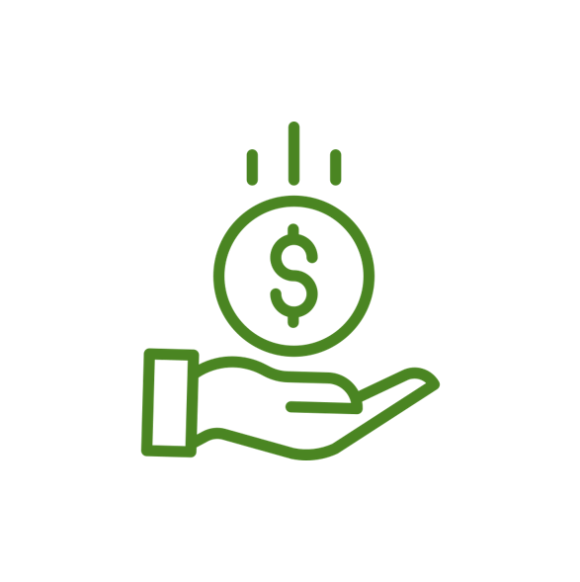
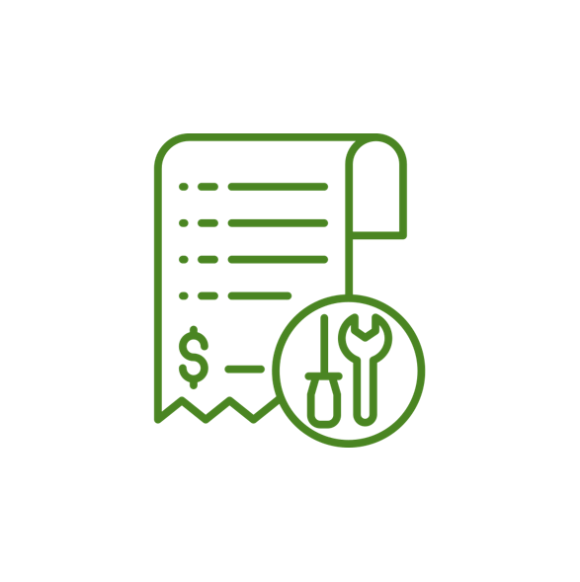
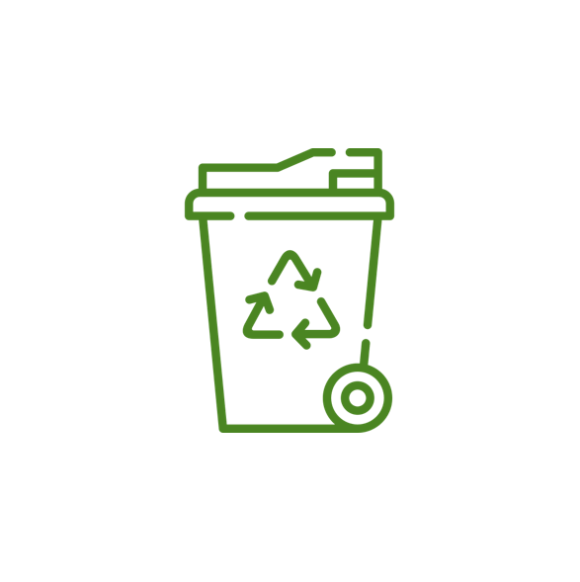
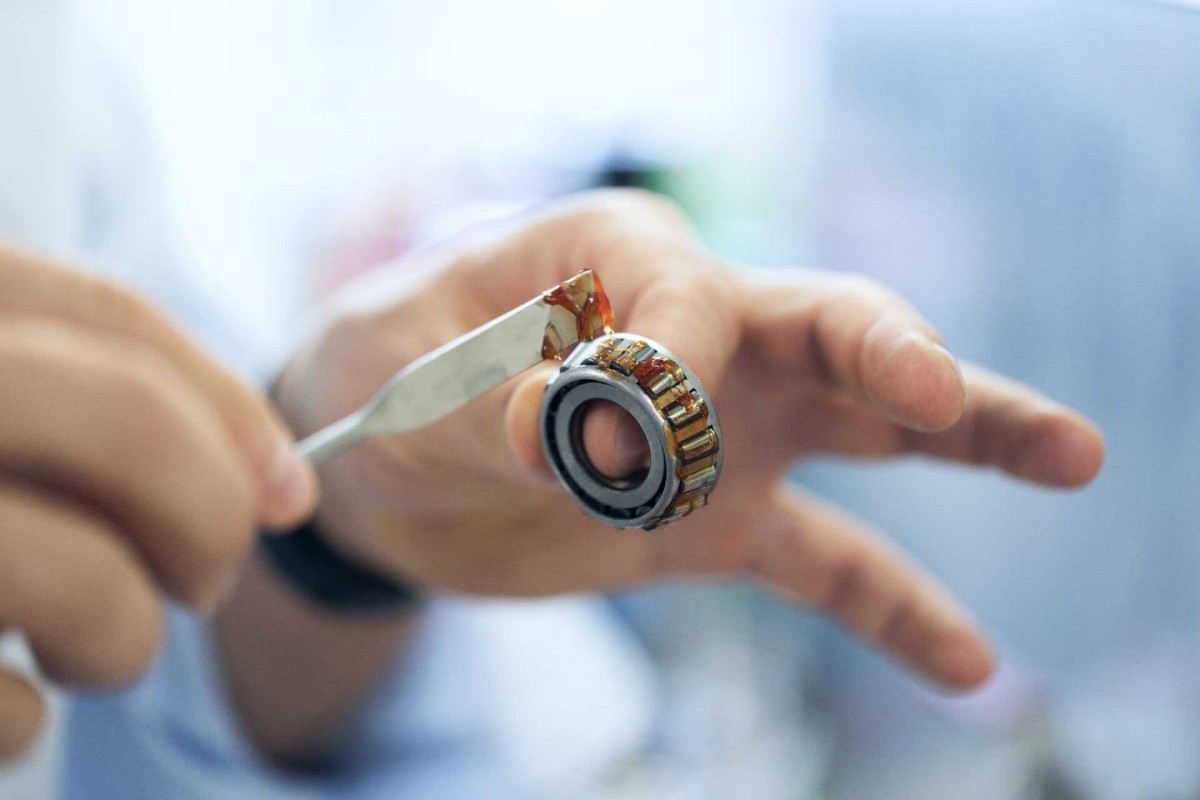
OMC₂ additive technology
The OMC2 additive technology (organic molybdenum compound), is also known under the terms PD (Plastic Deformation) or SE (Surface Engineering). What exactly does this technology do and what are its advantages?
The active complex of the OMC2 additive technology changes the structure of metal surfaces through a special micro-smoothing effect. This results in several advantages:
- The roughness of components is not rubbed off, instead they deform under load.
- The pressure absorption capacity of the surfaces increases strongly.
- In the micro range, flow smoothing occurs and thus friction losses and wear are significantly reduced.
Three-phase effect of OMC₂ technology
The stronger the pressure, the more effective the OMC₂ technology: as the load increases, the OMC₂ components migrate into the metal surface and lead to the special micro-smoothing effect of the surface structure. Unevenness is smoothed out and friction and wear on the components are extremely minimised. The following three diagrams illustrate how an OMC₂ lubricant acts on a surface:
Increasing the contact surfaces with OMC₂ technology
Without OMC₂ technology, the contact area between two friction surfaces is significantly smaller due to the surface roughness. Only the rough "tips" of the surfaces touch each other (see "before", exemplary visualisation on the left).
By using OMC₂ technology, sufficient lubricating films and a protective reaction layer are formed on the surfaces. The contact surface increases and the loads are distributed evenly (see "after", example visualisation on the right).
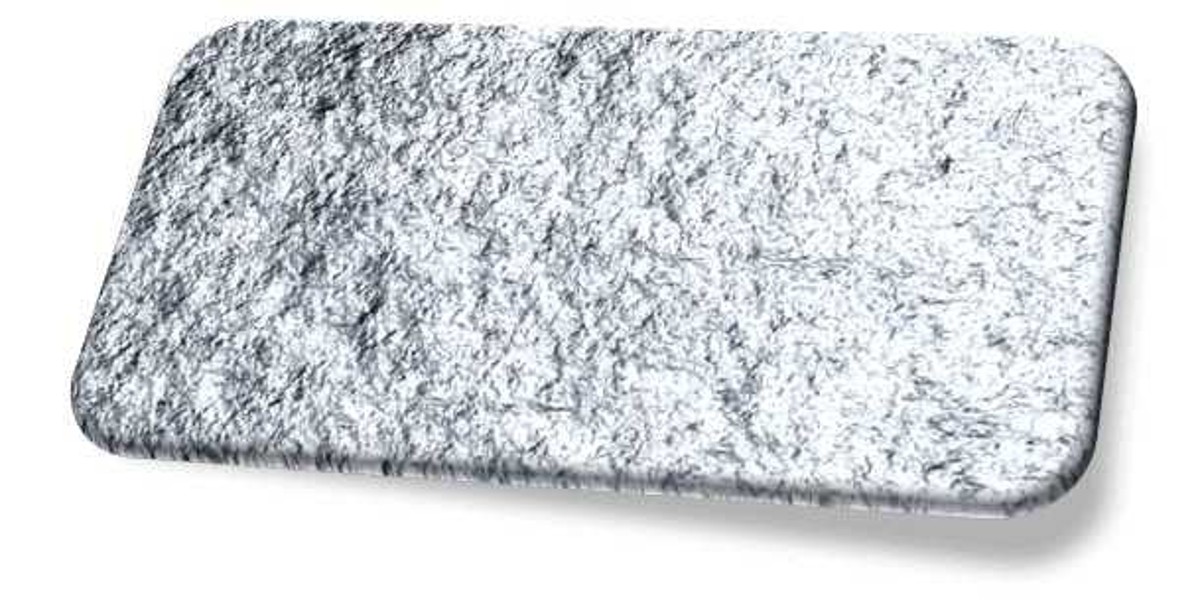
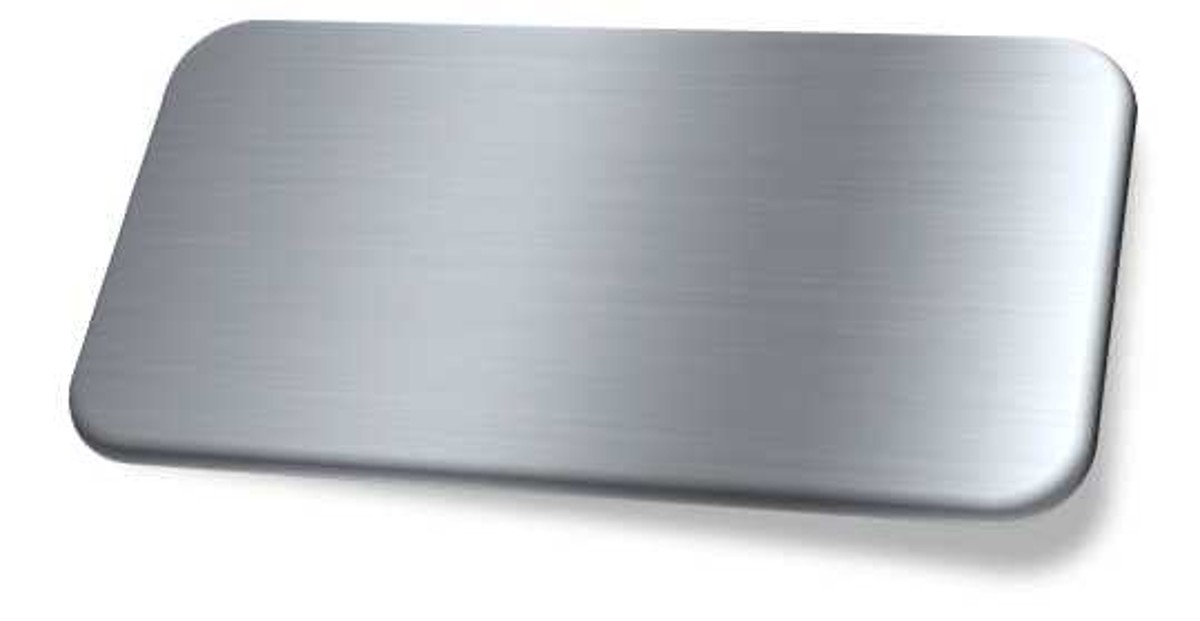
Test results and competitor comparisons
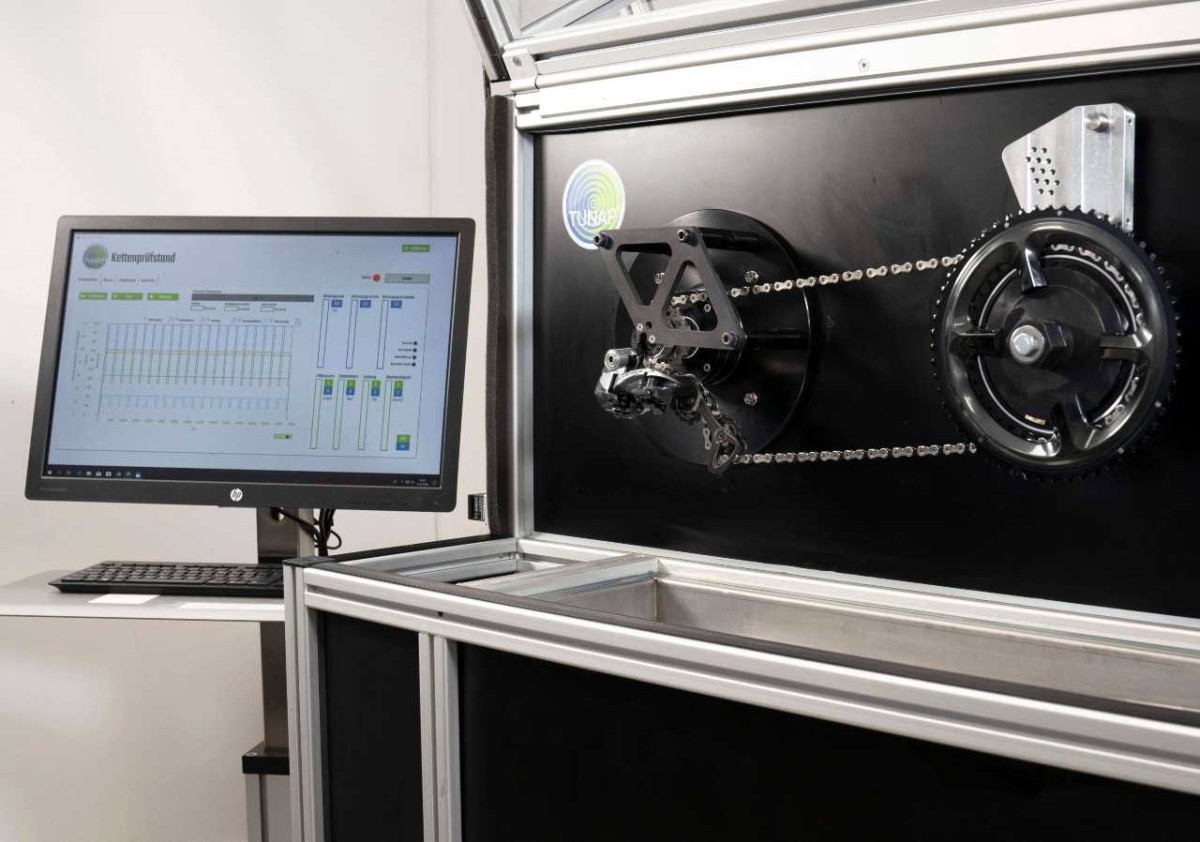
TUNAP two-wheel chain test bench AU 01.
Chain test bench
For OMC2 technology, we rely on high-quality raw materials, carefully matched formulations and continuous quality assurance. This enables us to meet the highest demands on lubricants.
In order to measure the efficiency of various lubricants on the chain and to provide verifiable data, we test them on our two-wheel chain test rig AU 01, among other things.
In addition to cadence, torque, power, gear ratio and speed, we particularly analyze the parameters of efficiency on our chain test stand. With the data obtained from these tests, lubricants can be developed that guarantee the highest performance quality.
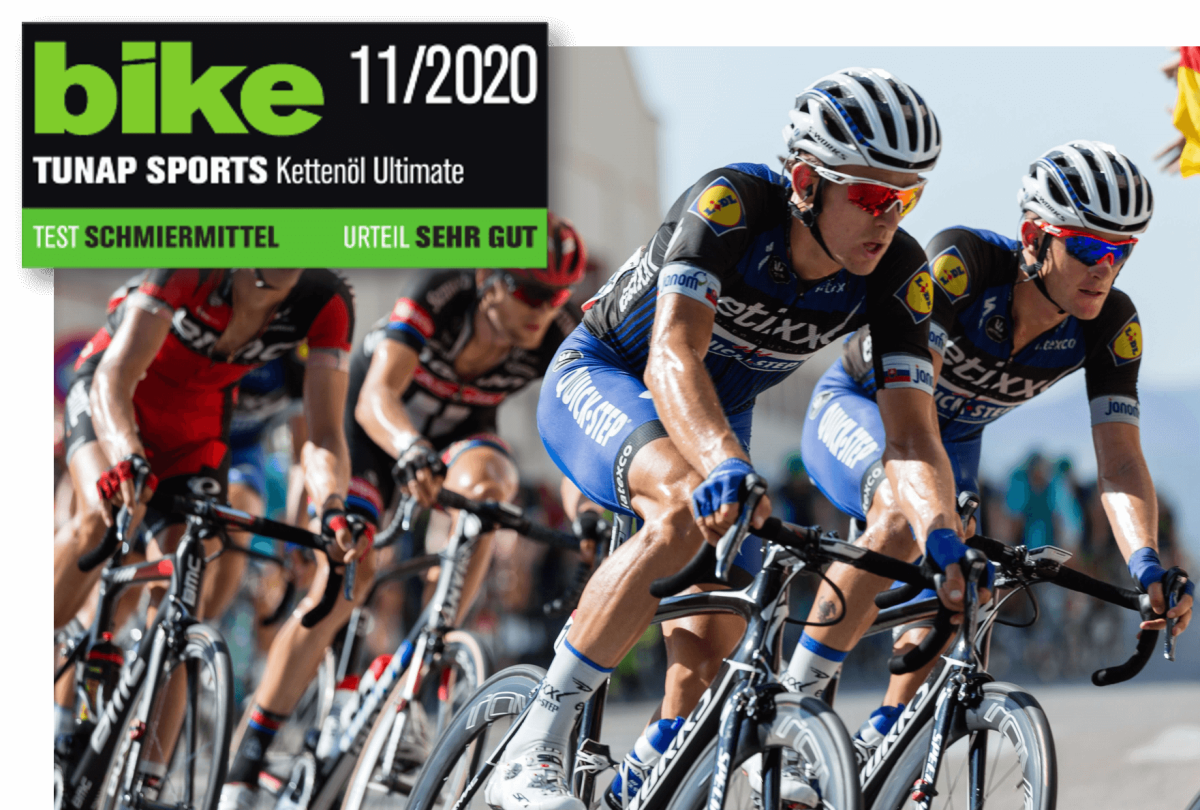
Test winner in German "BIKE" magazine: TUNAP Sports "Chain Oil Ultimate".
Bike race
We can simulate special stages or entire bike races on our chain test rig and draw conclusions as to which lubricant formulation is best suited to the distance to be covered.
Our tests show that the coefficient of friction can be reduced by up to 30% by using OMC2 technology. What does this mean in concrete terms? In a bicycle race over 155 miles, this could result in a time advantage of one minute and 46 seconds.
The latest test by the German "BIKE" magazine confirms the quality of our OMC2 technology: In issue 11/2020, 18 chain lubricants were tested for the criteria lubricity, creep ability, corrosion protection, dirt adhesion and handling. Conclusion: The TUNAP Sports "Chain Oil Ultimate" achieved the best result and was thus declared the test winner.
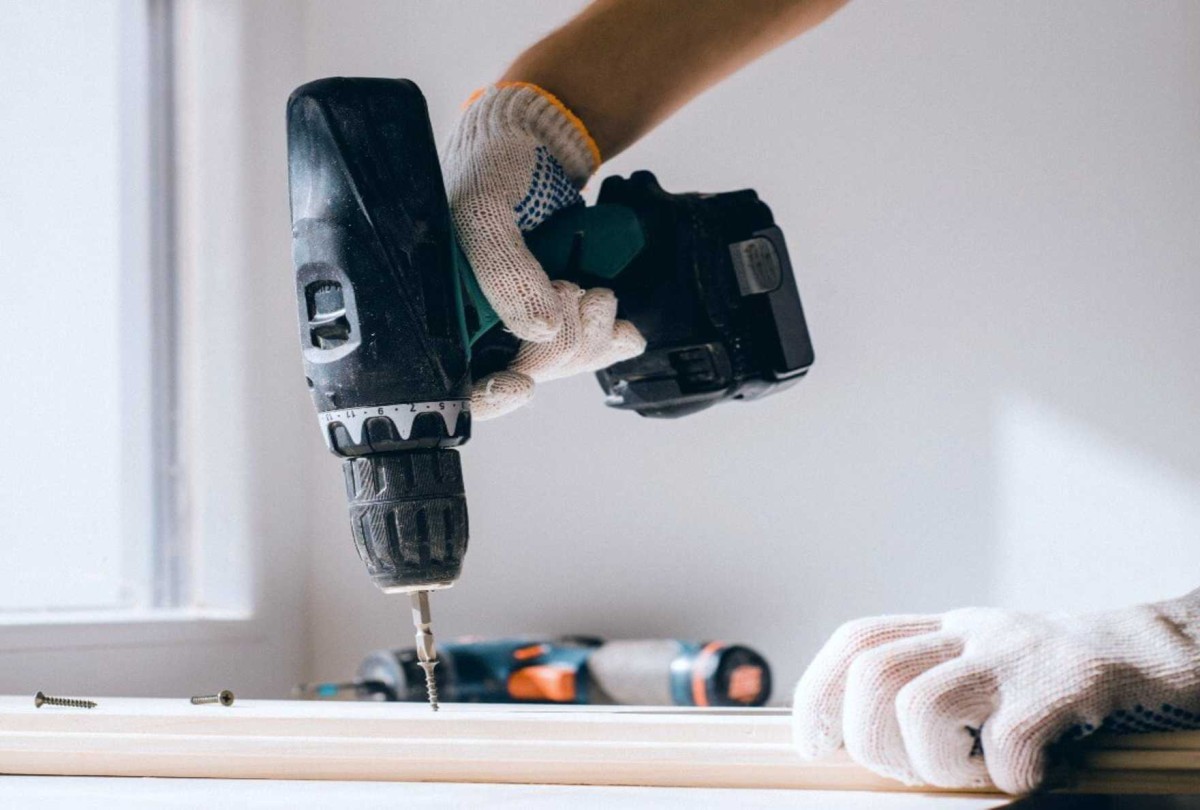
It runs and runs and runs... With TUNGREASE OMC2-2 plus lubrication, a power tool runs perfectly even after 250 hours continuous use.
Power tool in long-term test
In this long-term test, a cordless percussion drill ran with two different greases in continuous operation: first with the reference grease, then with TUNGREASE OMC2-2 plus. The result was clear: with the reference lubricant, the device failed after only 82 hours of operation. With TUNGREASE OMC2-2 plus, the device ran for well over 250 hours.
TUNGREASE OMC2-2 plus reaches a stable low level of power consumption much faster. This is due in part to the fact that this formulation is "dynamically light", i.e. it offers low resistance and facilitates movement. The OMC2 additive technology also reduces friction and thus heat generation, energy consumption and wear.
This is proof that lubrication with TUNGREASE OMC2-2 plus allows significantly longer operating times per battery charge.
Rolling bearing lubrication
The full potential of the OMC₂ additive technology can also be demonstrated using the example of rolling bearing lubrication on the FE8 test bench:
In a standard test procedure for the performance of lubricating greases in rolling bearings under realistic conditions, our TUNGREASE OMC₂-2 plus shows significantly lower wear values than lubricating greases from common competitors.
The average frictional torque, which is reduced by around 50 per cent both at start-up and during steady-state running, means considerable energy savings compared to conventional lubricants.
DIN 51819-2-C-75/50-40 |
TUNGREASE OMC₂-2 plus |
Competitors |
---|---|---|
Wear on rolling elements mw50 |
≤ 2 mg |
≥ 20 mg |
Cage wear mwk50 | ≤ 50 mg | ≥ 50 mg |
Average frictional torque at | ||
● start Mrs | ~ 8 Nm | ~ 15 Nm |
● persistence Mrb | ~ 3 Nm | ~ 11 Nm |